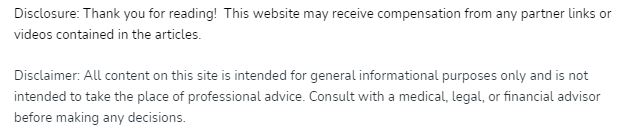
Screen printing is a versatile and popular printing technique widely used in various industries. This beginner’s guide introduces you to the basic concepts and techniques of screen printing, helping you to understand the process, the required materials, and how to get started with your projects.
What Materials and Tools Do I Need for Screen Printing?
Screen Printing Frames and Mesh
Choosing the right frame and mesh is foundational to successful screen printing. Frames come in different sizes and materials, like wood and aluminum, affecting durability and cost.
The mesh count determines the level of detail you can achieve; a higher mesh count is better for fine details, while a lower one suits bold designs.
Mesh also varies in thread type and thickness, which can affect ink flow and the final appearance of the print. Polyester is commonly used due to its practicality and durability. By understanding these elements, you can tailor your screen selection to the project’s specific needs.
Proper tension of the mesh on the frame is crucial to ensure sharp and accurate prints. Tight mesh aids in pushing the ink through efficiently, reducing smudging. Beginners should consider starting with pre-stretched frames to simplify setup and ensure consistent results.
Inks and Emulsions
Screen printing inks come in various formulations, such as water-based, plastisol, and discharge inks. Water-based inks are eco-friendly and ideal for softer prints, while plastisol inks provide vibrant colors but require more curing. The choice of ink should align with the fabric type and the intended durability of the print.
Emulsion acts as a stencil that holds the design on the screen. There are dual-cure and photopolymer emulsions, each catering to different exposure times and environmental conditions. The key is to select an emulsion that matches your light sources and screen preparation time.
Squeegees and Other Essential Tools
A squeegee is vital for forcing ink through the screen onto the printing surface. Different blade shapes and materials can affect the pressure and movement, thereby impacting the quality of the print. For detailed work, softer blades are preferable, whereas harder blades are better for bold prints.
Beyond squeegees, essential tools include scrubbers for cleaning screens, registration systems for aligning multi-color prints, and curing equipment like heat guns or flash dryers. These tools collectively contribute to a streamlined printing process. Investing in quality tools ensures consistent and professional results.
Effective organization of your tools can enhance the workflow. Each piece of equipment should be readily accessible and maintained regularly to avoid delays during printing sessions. Establishing a routine for tool maintenance will prolong their lifespan and improve print precision.
How Can I Start My First Screen Printing Project?
Design Preparation and Transfer
The initial step in screen printing is to create or select a design suitable for this method. Designs typically require simplification to account for the medium’s limitations. Once finalized, the design should be printed onto a transparent sheet, which will be transferred to the emulsion-coated screen using exposure to light.
During the exposure process, the light hardens the emulsion where it is not covered by the design. Unwanted areas are washed away, leaving a stencil through which ink will pass during printing. This step is critical in defining the sharpness and accuracy of the final print.
Successfully transferring the design involves correct exposure timing and placement. Using a test screen initially can help in adjusting variables before the final screen is prepared. This preparation is invaluable in foreseeing potential issues that could arise in actual printing.
Setting Up Your Printing Station
Creating a dedicated printing station at home or in a workspace ensures efficiency and orderliness in your screen printing process. Start by covering surfaces to prevent ink stains and setting up proper ventilation. Adequate lighting and storage for inks and tools should also be considered.
Organize your workstation so that all the necessary materials and tools are within arm’s reach. This setup minimizes disruption during the printing process. Having a clean and organized area also simplifies post-project cleanup and maintenance.
Ensuring that your station is ergonomically arranged can reduce physical strain and promote both precision and enjoyment during printing. Customizing your space with racks or shelves will help manage supplies and keep the workstation uncluttered. As you progress, the station can evolve to incorporate more advanced equipment.
Screen printing can be an exciting and rewarding skill to master, opening up endless possibilities for personal and professional projects. By understanding the materials and methods, anyone can begin creating unique and high-quality prints. This guide has provided you with the fundamental knowledge needed to get started in the world of screen printing.
.